10 Mastercam 2025 Features You Need to Know
- SA JBM
- Sep 10, 2024
- 3 min read
Mastercam 2025 is here to elevate your machining experience! With feedback from users and shops worldwide, we built upon our past advancements and are excited to bring you our most intuitive interface yet.
Increase your machining performance and reduce overall production costs with powerful toolpaths, turning enhancements, and more. Here are the top 10 new Mastercam 2025 features – and how they can help your shop.
1. Mastercam Deburr
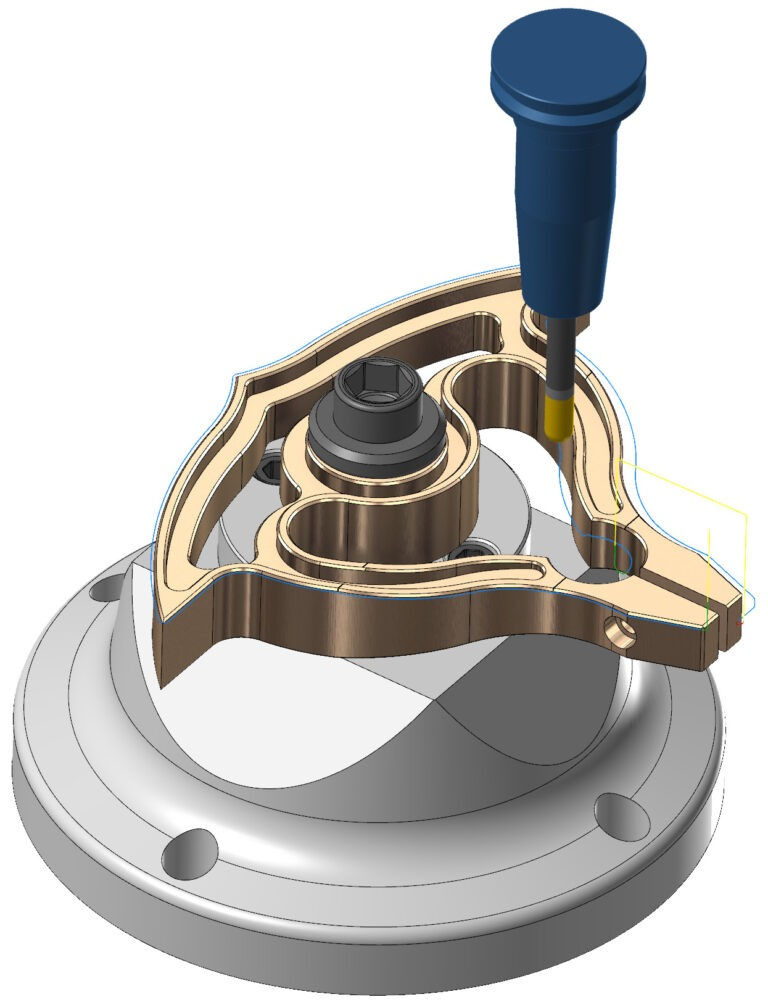
Mastercam Deburr toolpath simplifies the deburring process through automatic edge detection and intuitive controls. It was created so that users can take advantage of the streamlined Deburr cycle in a 3-axis environment without a Mastercam Multiaxis license.
2. Finishing Passes
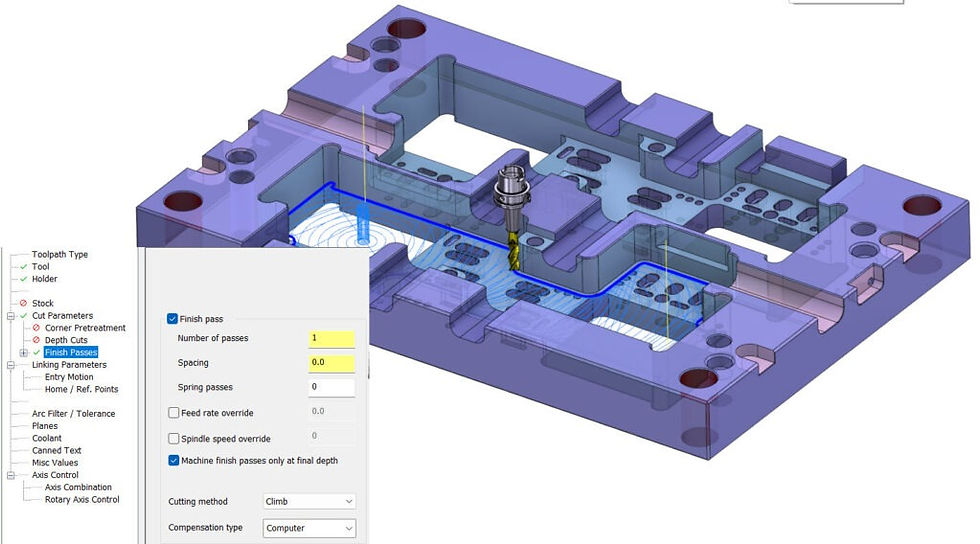
Mastercam 2025 introduces the ability to add Finish Passes to Mastercam 2D Dynamic Mill and Area Mill toolpaths. Use the new Finish Passes page to add high speed finishing passes along the selected boundaries of the toolpath. Other parameters on the page allow you to further define the finish pass, such as feed rate and spindle speed overrides.
3. Thread Mill Enhancements

Various enhancements have been added such as Speed/Feed Override for Lead In/Out which provides better control during entry moves, which promotes better tool life and more accurate machining of threads. Gradual Lead In/Out provides more control over the tool during engagement and disengagement. And the new Tool Edge Feed Rate calculates the feed rate based on the tool’s tangential edge rather than on the centerline.
4. Solid Hole Selection
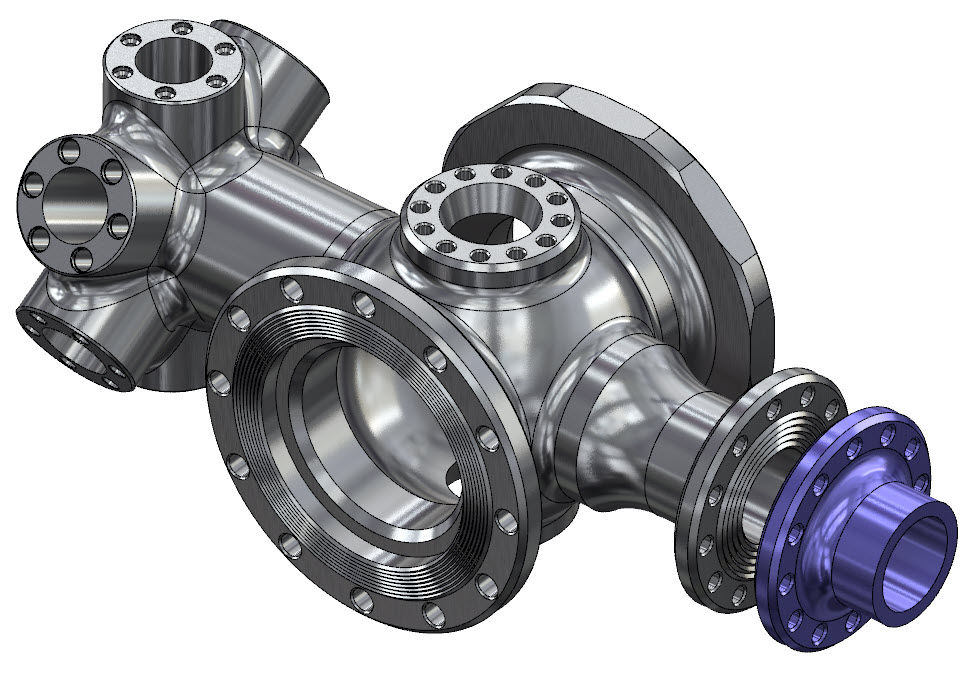
For those customers who use Hole Making and Process Hole toolpaths, Mastercam 2025 includes changes to the default selection behavior of the Solid Hole Selection and is therefore not optional. Create a more efficient, precise, and controllable hole selection.
5. Safety Zone Improvements for Hole Making

The new Safety Zone now uses meshes for parametric shapes. Along with an updated algorithm which results in the Safety Zone now being a post toolpath calculation, new parameters are now available including Linear Tolerance, Blending Distance, and Smoothing Distance.
6. Y-Axis Turning Support in Mastercam Mill-Turn

Mastercam 2025 introduces Mastercam Mill-Turn support for Y-axis Turning. All turning toolpaths except Custom Thread and B-axis Contour Turning support Y-axis functionality. Automatically create a set of planes that you can use to create your toolpath with the proper tool orientation and spindle origin. Approach and retract strategies have been enhanced to include Y-first strategies, along with the ability to designate tool assemblies as Y-axis compatible in the holder component page.
7. A-Axis Contour Turning in Mastercam Mill-Turn

The new A-axis Contour Turning toolpath complements the B-axis Contour toolpath introduced in Mastercam 2023 and extends support for rotary contour turning. The new toolpath is very similar to the B-axis Contour toolpath except that it uses Y-axis tools. The ability to rotate the tool while in the cut lets users reach difficult-to-machine areas while taking advantage of the latest advances in Y-axis tool technology.
8. B-Axis Contour Turning Enhancements

Two new features have been added to the B-axis Rotary Contour toolpath in Mastercam Mill-Turn. You can now include splines in your chained geometry which will simplify and speed up the toolpath generation process. In addition, new tool angle controls let you specify either a leading or trailing angle for the insert, which enhances the toolpath creation process and greatly improves the resulting machined finishes.
9. Analyze Deviation Function

Analyze Deviation analyzes the differences between entities and applies a color coded “heat map” to the geometry, which displays deviations within the graphics window. Analyze Deviation allows you to compare any combination of points, curves, surfaces, bodies, or faces.
10. Machine Configuration Save/Load in Mastercam Mill-Turn

Mastercam Mill-Turn platform users can now store and reuse common machine setups, including work holding, tool holding, and tooling components. Save specific machine configurations to individual configuration files, then load them again to quickly use the same setup on additional parts.
Commenti